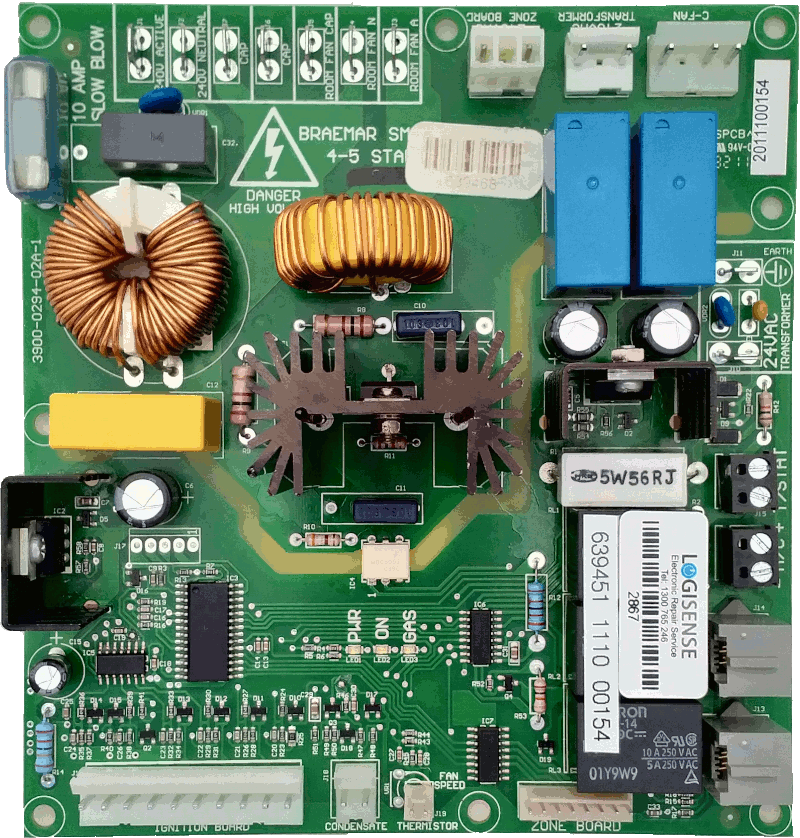
Braemar 639468 Smart Control (BSC) 4-5 STAR PCB
No Longer Available. Why?
Common faults:
- False overheat fault (Code 10 or Code 19),
- False ignition failure fault (Code 7),
- False EFS shutdown fault (Code 11),
- Incorrect thermistor temperature,
- False thermistor faults (Code 4, 5, 15, 16),
- Fan starts at full speed,
- Fan speed not adjustable,
- False condensate detected at start fault (Code 18).
Braemar Smart Control Fault Codes (4-5 STAR Models):
Code | Fault Description |
01 | Pressure switch P-55 closed at start. This fault is usually caused by a faulty Fenwal ignition module. |
02 | Pressure switch P-55 failed to close. Check the following:
|
03 | Pressure switch P-55 open during run. Check everything as per fault code 02. |
04 | Thermistor temperature higher than 70C during run. Check the following:
If overheating issues can be ruled out, the BSC PCB may be faulty. |
05 | Thermistor not connected or short circuit. Check the resistance of the thermistor while disconnected from the BSC PCB. The thermistor should measure around 3.3KΩ at 25C. If the thermistor is shorted or open-circuit, replace the thermistor. If the thermistor tests OK, then this will most likely be due to a faulty BSC PCB. |
06 | Over temperature switch OT4 open (5-star models only). Check for overheating conditions as per fault code 04. |
07 | Ignition failure – Possible faulty/dirty flame sensor or false fault due to BSC PCB fault. Check the following:
|
08 | Condensate detected at start (5-star models only). Check that the condensate drain is not blocked and that the heater is sitting on a level surface. To troubleshoot models that use a condensate probe, try disconnecting the condensate sensor from the BSC PCB. If the fault goes away, the heat exchanger may be full of water, or the condensate probe may be touching some debris inside the heat exchanger, allowing current to flow to earth, which will be detected as condensate. If the fault persists with the condensate probe disconnected, the BSC PCB is most likely faulty. Note that disconnecting the condensate sensor will not work on models that use a pressure switch for condensate sensing. For models that use a pressure switch for condensate sensing, check that the vacuum hoses are clear of condensate buildup (water) and other blockages. |
09 | Internal memory failure – This is due to a faulty BSC PCB. |
10 | Over temperature switch HX OT1 open (tripped) – Can be a faulty over-temp switch or BSC PCB fault. Check for problems that may cause overheating (refer to code 04). |
11 | EFS shutdown – The Fenwal ignition module has shut down or the BSC PCB may be faulty. This fault can be produced by a number of causes. Check the following:
|
12 | Pressure switch P-100 closed at start. This fault is usually caused by a faulty Fenwal ignition module. |
13 | Pressure switch P-100 failed to close. |
14 | Pressure switch P-100 open for more than 30 seconds during run. |
15 | Thermistor in cool location in duct – If the heater previously worked, it may be a faulty thermistor or faulty BSC PCB. Check the resistance of the thermistor (refer to code 05). If the thermistor tests OK, it will most likely be due to a BSC PCB fault. |
16 | Thermistor not installed in outlet duct – If the heater previously worked, the thermistor may be faulty, the BSC PCB may be faulty, the fan may not be running at the correct speed, fan run capacitor may be degraded. Test the thermistor (refer to code 05) and then run through the over-temperature checklist to rule out airflow issues (refer to code 04). |
17 | Condensate detected during run – Blocked condensate drain, heater not level, faulty BSC PCB. |
18 | Condensate detected at start. If this fault occurs on 4-star models that don’t have a condensate sensor, this fault is due to a faulty BSC PCB. If this fault occurs on a 5-star model, refer to code 08 for possible solutions. If no cause is found, the BSC PCB is likely faulty. |
19 | Over temperature switch HX OT2 open at start – Usually due to a faulty BSC PCB but can be caused by overheating issues. Check for possible causes of overheating (refer to code 04). |
Terms & Conditions – Repair/Exchange:
- All products come with a standard 12 month warranty, that can be extended at the time of sale. Extended warranties are available at a rate of $44.00 per every additional 6 months. The warranty period is limited to a maximum of 24 months.
- The warranty covers all parts used in the repair as well as the labour provided by LOGISENSE. The warranty does not cover the labour of yourself or any third party.
- The warranty does not cover damage caused by faulty accessories, power surges, lightning, water ingress, wiring faults or incorrect installation.
- The customer pays all postage costs (where applicable) and should ensure that all items posted are adequately protected with bubble wrap or similar.
- Items that have been tampered with (eg. items that have been previously repaired/worked on by yourself or any 3rd party), cleaned with chemicals, damaged by water/liquid/moisture ingress, fire, power surges/spikes, lightning or that are in otherwise poor physical condition are not eligible for exchange, but a repair may be offered depending on the extent of the damage. Items that meet this criteria need to be assessed on a case-by-case basis and may attract an additional fee, as they typically require more labour and components than usual to complete the repair. It is also possible that the repair request may be declined.
- There is an assessment fee of $44.00 if the item you bring/send for repair is not faulty.
- There is no charge in the event that the repair is unsuccessful or the item sent in for repair is deemed to be unviable to repair, other than return postage (if applicable). Such items can be disposed of via e-waste recycling.
Terms & Conditions – Advance Exchange:
- Advance exchanges are only available to trade customers that have established a working relationship with us.
- Advance Exchange is not available for all products. This includes, but is not limited to, Breezair ICON (110547, 110554, 112954, 114675, etc) control modules and Bonaire EAC 200x (PNE) control boards.
- Faulty item(s) must be returned or shipped back to us within 28 days of the invoice date.
- The customer is to pay any costs associated with the return of the faulty item(s) and will not be reimbursed for these costs.
- Items that have been tampered with (eg. items that have been previously repaired/worked on by yourself or any 3rd party), cleaned with chemicals, damaged by water/liquid/moisture ingress, fire, power surges/spikes, lightning or that are in otherwise poor physical condition are not eligible for exchange.
- Advance exchange deposits will only be refunded upon receipt of the faulty item(s) and only if the returned item(s) meet the conditions outlined above.
Terms & Conditions – Returns:
- Reconditioned electrical/electronic parts/assemblies may be returned but will be subject to a $44.00 restocking fee. If any returned parts/assemblies are damaged, no refund will be offered.
All trademarks are the property of their respective owners.