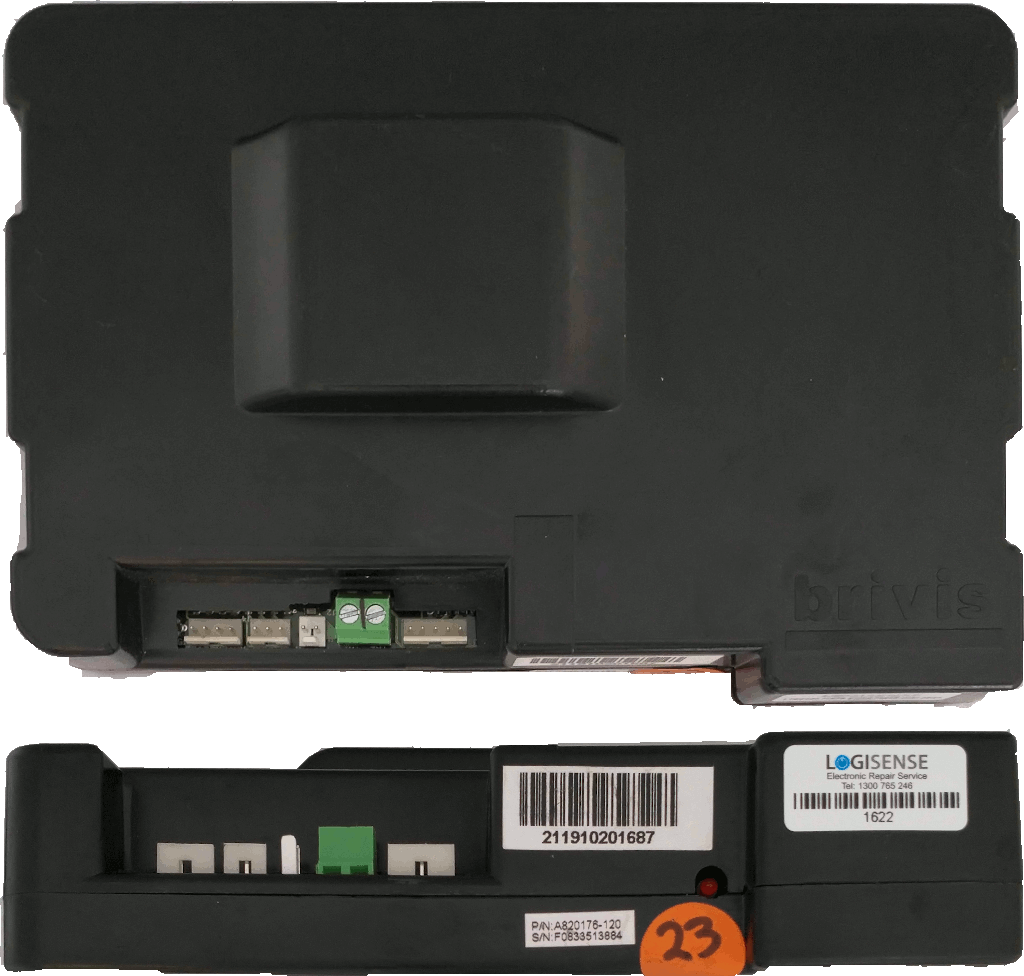
Brivis N-E3/N-E5/N-E6 Evaporative Cooler Module
Repair Price: Not Available
Warranty: 12 months, extendable to 18 or 24 months.
Common faults:
- Not filling with water,
- Water overflowing,
- Unable to move damper motor assembly,
- No power to Networker,
- No communication with Networker,
- Unable to sense water,
- LED not illuminated,
- No fan speed control,
- Fan stuck on high speed,
- Water inlet solenoid humming when cooler not in use.
Brivis Evaporative Cooler Fault Codes:
Code | Fault Description |
“Dead” | No Power – There’s an 8A ceramic slow-blow 3AG fuse inside the control module. Turn off and disconnect the mains power from the cooler, remove the control module and carefully open it, then check the fuse using a multimeter set to continuity or ohms measurement mode to confirm that the fuse has not blown. If the fuse has blown, the most likely cause is a faulty fan motor. |
Overflowing | If the cooler is overflowing or the water inlet solenoid valve will not turn off, the most likely causes are a faulty water sensor or faulty control module (unable to sense water at high level). |
ServoSeal not operational | Both the ServoSeal assembly and the control module can be the cause of this problem. You may find that the ServoSeal is stuck in one position (open or closed) or that it is vibrating. If the ServoSeal arm is gently vibrating, this is a sign of a control module fault. |
30 | FAN_LIMP – The fan may not be running, not running at the correct speed or there may be no signal coming from the fan speed sensor. The speed sensor is located on the back of the fan motor. It may stop working if it becomes detached from the motor or if dirt/dust builds up inside the sensor. |
40 | The low level water sensing has failed. This can be due to a faulty water sensor or a control module fault. Test the water sensor by checking for continuity between each water sensing plate and a wire in the plug and try cleaning the water sensor (brush and soapy water, rinse thoroughly afterwards). |
41 | The high level water sensing has failed. This can be due to a faulty water sensor or a control module fault. Test the water sensor by checking for continuity between each water sensing plate and a wire in the plug and try cleaning the water sensor (brush and soapy water, rinse thoroughly afterwards). |
42 | The water is unable to be drained from the cooler. This could be due to a blocked drain or inoperative ServoSeal. The control module may also be faulty, causing it to be unable to operate the ServoSeal. If the cooler has drained, try cleaning the water sensor, as a dirty sensor could cause the control module to think that water is still present when it isn’t. |
50 | Unable to detect water. After opening the solenoid valve to allow water into the cooler, there was no water detected after 15 minutes. Check that the water supply to the cooler is on and that power is getting to the solenoid valve when the cooler is turned on and in cool mode. Check that water isn’t draining from the cooler (this may be due to a faulty ServoSeal or faulty control module). If the cooler is filling with water or overflowing, the water sensor may be faulty or the control module may have a fault in the water sensing circuitry. |
60 | MOTOR_OC – The fan motor is open-circuit. This can occur if the fan motor has overheated and the internal thermal protection has been triggered. If the fan motor is not open-circuit, then it is likely to be a faulty control module. |
LED Flashes | Fault Description |
4 | Water not detected at high level. The water sensor has detected water at the low level, but has not detected water at the high level. Check that each of the plates of the water sensor have continuity to one of the wires in the plug at the end of the water sensor cable. If the water sensor is found to have continuity and the cooler is overflowing with water, then the water sensing circuitry in the control module has likely failed. |
6 | Water not detected at low level. The cooler has energised the water inlet solenoid valve but water has not been detected by the water sensor at the low level (timeout is approx. 10 minutes). This may be caused by a faulty damper, causing all water to drain out of the cooler as it tries to fill. The damper assembly may also be vibrating, due to a control module fault, which will cause it to get stuck in either the open or closed position. This fault can also be caused by a faulty solenoid valve (burnt out or seized in the closed position), faulty water sensor or faulty water sensing circuitry in the control module. Check that each of the plates of the water sensor have continuity to one of the wires in the plug at the end of the water sensor cable. If the water sensor is found to have continuity and the cooler is overflowing with water, then the water sensing circuitry in the control module has likely failed. The cooler may also run the fan and blow hot air when this failure occurs. |
7 | Fan Motor Open Circuit. The fan motor is open circuit, most likely due to the fan motor overheating and tripping the thermal protection mechanism inside the motor. This may be due to a degraded fan motor run capacitor (check capacitance), or a short circuit inside the fan motor. |
Terms & Conditions – Repair/Exchange:
- All products come with a standard 12 month warranty, that can be extended at the time of sale. Extended warranties are available at a rate of $44.00 per every additional 6 months. The warranty period is limited to a maximum of 24 months.
- The warranty covers all parts used in the repair as well as the labour provided by LOGISENSE. The warranty does not cover the labour of yourself or any third party.
- The warranty does not cover damage caused by faulty accessories, power surges, lightning, water ingress, wiring faults or incorrect installation.
- The customer pays all postage costs (where applicable) and should ensure that all items posted are adequately protected with bubble wrap or similar.
- Items that have been tampered with (eg. items that have been previously repaired/worked on by yourself or any 3rd party), cleaned with chemicals, damaged by water/liquid/moisture ingress, fire, power surges/spikes, lightning or that are in otherwise poor physical condition are not eligible for exchange, but a repair may be offered depending on the extent of the damage. Items that meet this criteria need to be assessed on a case-by-case basis and may attract an additional fee, as they typically require more labour and components than usual to complete the repair. It is also possible that the repair request may be declined.
- There is an assessment fee of $44.00 if the item you bring/send for repair is not faulty.
- There is no charge in the event that the repair is unsuccessful or the item sent in for repair is deemed to be unviable to repair, other than return postage (if applicable). Such items can be disposed of via e-waste recycling.
Terms & Conditions – Advance Exchange:
- Advance exchanges are only available to trade customers that have established a working relationship with us.
- Advance Exchange is not available for all products. This includes, but is not limited to, Breezair ICON (110547, 110554, 112954, 114675, etc) control modules and Bonaire EAC 200x (PNE) control boards.
- Faulty item(s) must be returned or shipped back to us within 28 days of the invoice date.
- The customer is to pay any costs associated with the return of the faulty item(s) and will not be reimbursed for these costs.
- Items that have been tampered with (eg. items that have been previously repaired/worked on by yourself or any 3rd party), cleaned with chemicals, damaged by water/liquid/moisture ingress, fire, power surges/spikes, lightning or that are in otherwise poor physical condition are not eligible for exchange.
- Advance exchange deposits will only be refunded upon receipt of the faulty item(s) and only if the returned item(s) meet the conditions outlined above.
Terms & Conditions – Returns:
- Reconditioned electrical/electronic parts/assemblies may be returned but will be subject to a $44.00 restocking fee. If any returned parts/assemblies are damaged, no refund will be offered.
All trademarks are the property of their respective owners.